Introduction:
In today's highly competitive business landscape, maintaining consistent quality and ensuring customer satisfaction are paramount to the success and longevity of any organization. These two aspects go hand in hand and form the foundation for building a loyal customer base and fostering long-term relationships with clients.There are hundreds of way to address this. Few of them are summarized below:

100 ways :
Here are 100 ways to avoid process and product failure on the shop floor to maintain consistent quality and customer satisfaction:
1. Implement rigorous quality control measures
2. Conduct regular audits of production processes
3. Train employees on quality standards and best practices
4. Use effective inspection tools and techniques
5. Implement a robust supplier quality management system
6. Conduct thorough supplier audits
7. Establish clear quality requirements for suppliers
8. Monitor and address quality issues with suppliers promptly
9. Conduct regular maintenance of equipment and machinery
10. Implement preventive maintenance schedules
11. Ensure proper calibration of measuring instruments
12. Implement a comprehensive training program for operators
13. Provide ongoing training and skill enhancement programs for employees
14. Set clear quality goals and targets
15. Monitor key performance indicators (KPIs) regularly
16. Implement statistical process control techniques
17. Conduct root cause analysis for quality issues
18. Implement corrective and preventive action plans
19. Communicate quality goals and targets to employees
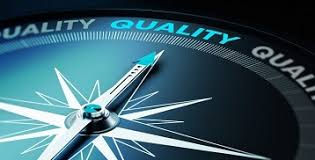
20. Foster a culture of continuous improvement
21. Encourage employee feedback on quality improvements
22. Implement a robust document control system
23. Regularly review and update standard operating procedures (SOPs)
24. Implement a robust change management process
25. Conduct regular process risk assessments
26. Implement controls to prevent non-conforming materials from entering the production line
27. Conduct regular material inspections and testing
28. Implement a robust product traceability system
29. Implement effective stock management practices
30. Conduct regular inventory audits
31. Implement proper handling and storage practices for materials
32. Establish clear protocols for handling customer complaints
33. Document and investigate customer complaints promptly
34. Take prompt corrective actions to address customer complaints
35. Conduct regular customer satisfaction surveys
36. Analyze customer feedback to identify areas for improvement
37. Monitor customer satisfaction trends and take corrective actions as needed
38. Implement effective change control procedures
39. Conduct thorough impact assessments for process changes

40. Involve relevant stakeholders in change management processes
41. Conduct regular safety inspections on the shop floor
42. Implement effective safety training programs for employees
43. Ensure adherence to safety protocols and procedures
44. Conduct regular safety drills and exercises
45. Establish a robust waste management system
46. Implement recycling and reusing initiatives
47. Monitor energy consumption and implement energy-saving measures
48. Implement effective environmental management practices
49. Conduct regular environmental audits
50. Establish clear guidelines for workplace organization and cleanliness
51. Implement 5S practices (Sort, Set in Order, Shine, Standardize, Sustain)
52. Implement visual management tools and techniques
53. Establish clear guidelines for equipment layout and positioning
54. Implement error-proofing techniques, such as poka-yoke
55. Conduct regular equipment performance evaluations
56. Implement effective changeover procedures
57. Conduct regular throughput analysis to optimize production flow
58. Implement effective production scheduling techniques
59. Monitor on-time delivery performance
60. Implement effective order tracking systems
61. Implement effective process control systems
62. Conduct regular process capability studies
63. Implement error detection and prevention systems
64. Establish clear quality gates at critical process stages
65. Conduct regular supplier performance evaluations
66. Establish clear communication channels with suppliers
67. Implement effective risk management practices
68. Conduct regular industry benchmarking studies
69. Implement effective cost control measures
70. Conduct regular cost of quality analysis
71. Implement effective product lifecycle management practices
72. Conduct regular product performance evaluations
73. Implement effective serialization and labeling practices
74. Conduct regular equipment validation and qualification studies
75. Implement effective inventory control systems
76. Monitor and control product shelf life
77. Implement effective root cause analysis techniques
78. Establish a continuous improvement feedback loop with customers
79. Conduct regular production process simulations and testing
80. Implement effective capacity planning and resource allocation techniques
81. Monitor and control variation in production processes
82. Implement effective employee performance evaluation systems
83. Conduct regular leadership and management training programs
84. Establish clear communication channels between management and shop floor employees
85. Implement effective employee engagement initiatives
86. Conduct regular employee satisfaction surveys
87. Implement effective supplier performance evaluation systems
88. Establish clear supplier communication channels
89. Conduct regular supplier collaboration and improvement meetings
90. Implement effective project management practices for process improvement initiatives
91. Establish clear goals and objectives for process improvement initiatives
92. Monitor and control project timelines and budgets
93. Conduct regular project status reviews and updates
94. Implement effective change communication and training programs
95. Conduct regular employee recognition and reward programs
96. Implement effective data collection and analysis techniques
97. Establish clear key success factors for process improvement initiatives
98. Monitor and control progress towards project goals
99. Implement effective data visualization and reporting techniques
100.
Celebrate and communicate successes achieved through process improvement initiatives
Remember, this is just a starting point, and you can customize and prioritize these strategies based on the specific needs and requirements of your organization.

Written by:
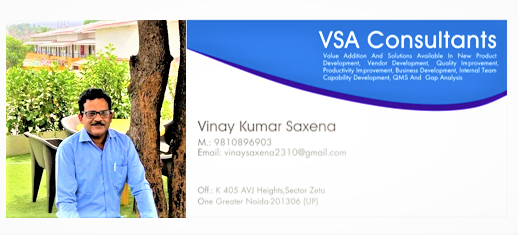
Very well compiled all methodology of customer satisfaction and manufacturing quality improvement. Most important points to improve customer satisfaction are maintaining and improving product quality, ontime delivery and
accepting and improving upon customer feedback
Thank you
Ashwani Pandey
Great very well consolidated and covered every aspect of Quality
An article which has covered every aspect of delivering a quality and reliable product or service which helps in building customer relationship...Quality should act as a part of profit centre...All the best..👍
GREAT 👍
Great